The Precast Story
Reaching a facility delivery timeline of 150 days
The Premise - 2020
At Godwitt, we believe in continuous innovation in all aspects of our operations. In 2020, having developed 1 million square feet of industrial space using conventional methods, we faced challenges with skilled labor shortages and prolonged facility delivery timelines for our occupiers. Hence we decided to upgrade our product - our journey towards the same began with a following realization that traditional construction methods were not meeting our quality standards or our facility delivery timelines
The Pilot Project - early 2021
In early 2021, we embarked on a pilot project to explore the prefabricated construction methodology utilising precast concrete elements. This initiative aimed to address both the issues while enhancing efficiency. Through meticulous planning and collaboration, we successfully completed a 0.1 million square feet standalone facility, gaining valuable insights into the supply chain and operational nuances of this new construction approach. we sucessfully leased the facility to occupiers like Nykaa Cosmetics and Amneal Pharmaceuticals
First production level precast facility - by 2022
Building on our learnings, we undertook our next challenge in 2022: developing a deep storage and warehousing facility near the Pipavav port region using the prefabricated construction methodology. Despite initial hurdles, we surpassed expectations by completing the project in just 166 days, setting a new industry benchmark for speed and quality
First industrial park integrating precast construction - in 2023
Buoyed by our success, we expanded our vision in 2023 with the launch of Soko by Godwitt - Khoda, India's first industrial park built entirely using precast concrete elements. With a focused goal of 150 days for facility delivery timeline, we not only met but exceeded our target. Additionally, securing an manufacturing based occupier, further validated the effectiveness of our approach
Taking precast production inhouse - early 2024
By early 2024, we had completed multiple projects totalling 0.75 million square feet of development. To ensure sustainability and autonomy, we took a crucial step this year of bringing precast concrete production in-house, and consolidating our position when it comes to the domain of industrial developments under the prefabricated construction methodology utilising precast concrete elements.
Our Design Philosophy
Explore our Standard building specification
Buoyed by our success, we expanded our vision in 2023 with the launch of Soko by Godwitt - Khoda, India's first industrial park built entirely using precast concrete elements. With a focused goal of 150 days for facility delivery timeline, we not only met but exceeded our target. Additionally, securing an manufacturing based occupier, further validated the effectiveness of our approach
Roofing
Leak-proof standing-seam roofing system made of color-coated galvalume, equipped with 13 mm XLPE insulation to maintain a temperature differential of 4-5 degrees Celsius between internal and external environments.
Cladding
Utilizing color-coated galvalume sheeting with 9 mm XLPE insulation to ensure a temperature differential of 4-5 degrees Celsius between external and internal environments.
Flooring
FM-2 flooring designed to withstand a uniformly distributed load of 6 tons per sq. meter. Panels feature a tolerance level of +/-10 mm, each measuring 3 meters in length.
.webp)
Canopy
Featuring a 5.00-meter-wide cantilever canopy extending from the loading docks or running dock edge, offering a clear height of 5.5 meters from the apron level.
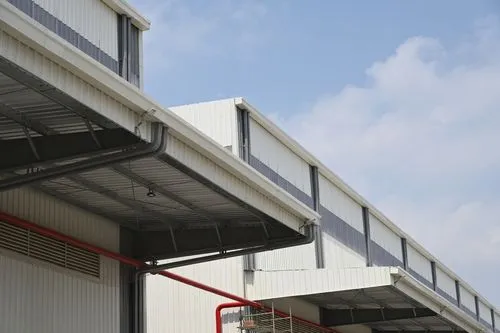
Wall
3 meter high precast walls, ensuring sturdy enclosure. Gaps between the color-coated sheets and walls if any, are filled with sealant like PU foam for durability.
.webp)
Emergency exit doors
2 hours fire rated, steel doors with panic bars as per the statutory norms; equipped with steps and railings leading to ground level and shall be located not more than 100 feet radius.
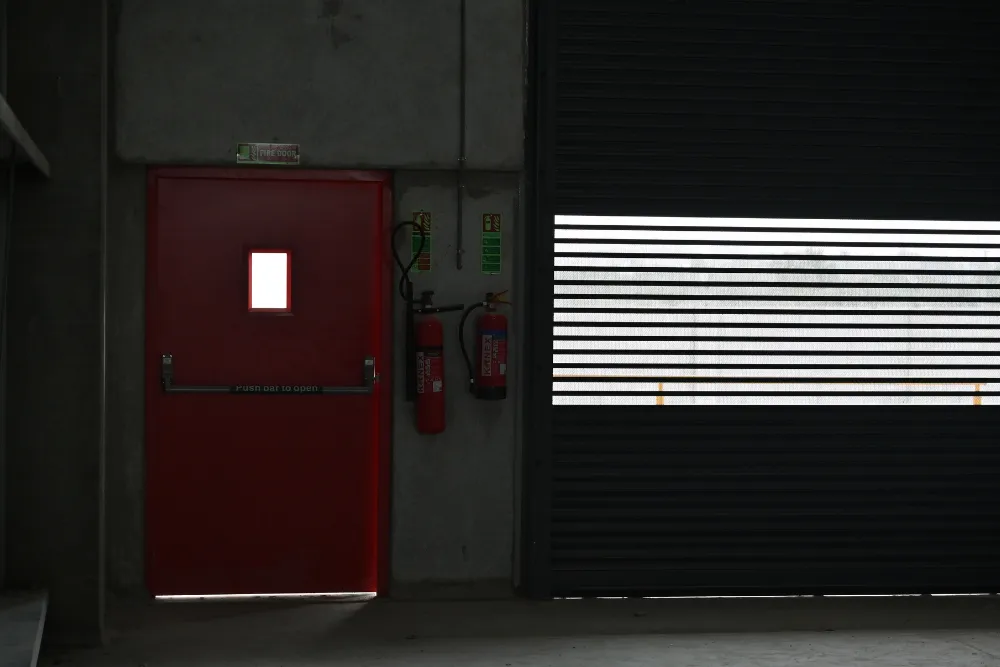
Insulation design
Utilizing advanced materials like XLPE insulation of 13mm and 9mm thickness, on roofing and cladding helps maintain a 4-5°C temperature difference internally.
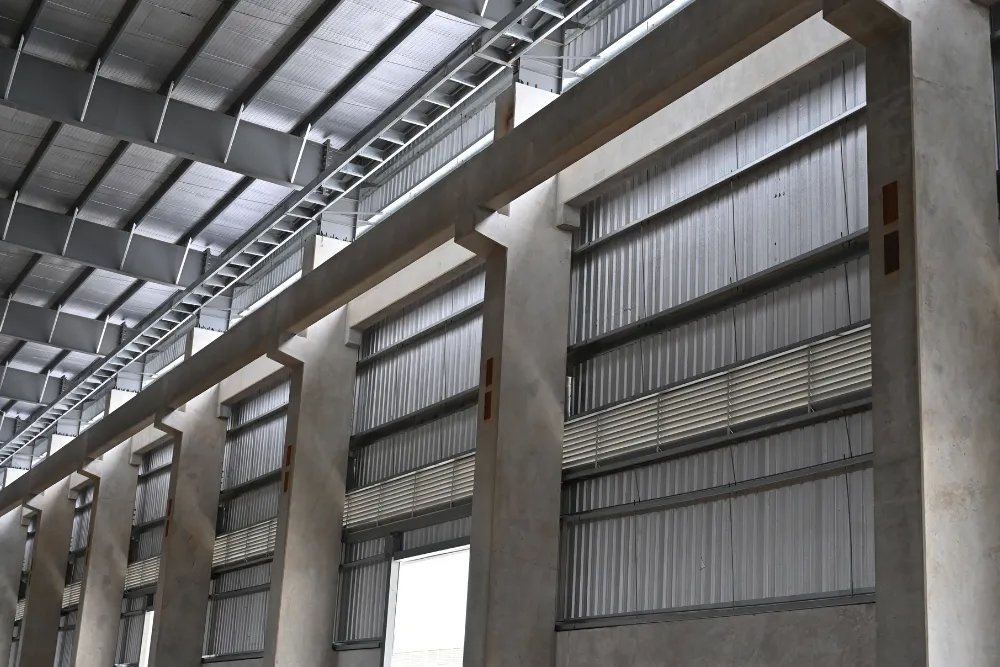
Washroom
Sufficient and separate modular washrooms and urinals will be provided, opening from within the building, with an 80:20 male to female ratio. The location will be determined, featuring ceramic tile flooring, glazed ceramic tile dado, and wooden flush doors.
Water tap-off
Water tap-off connection will be provided, at locations to be decided at a later stage.
Green is our blood
We as an organiation have a pro-green philosophy, which is why we have also taken up extensive green initiatives by introducing the Miyawaki plantation in our parks which accounts for 5% of our park area.
This leads to the integration of indigenous trees in our parks that encourage the native population of flora and fauna to organically create spaces that make our parks more than just industrial spaces.
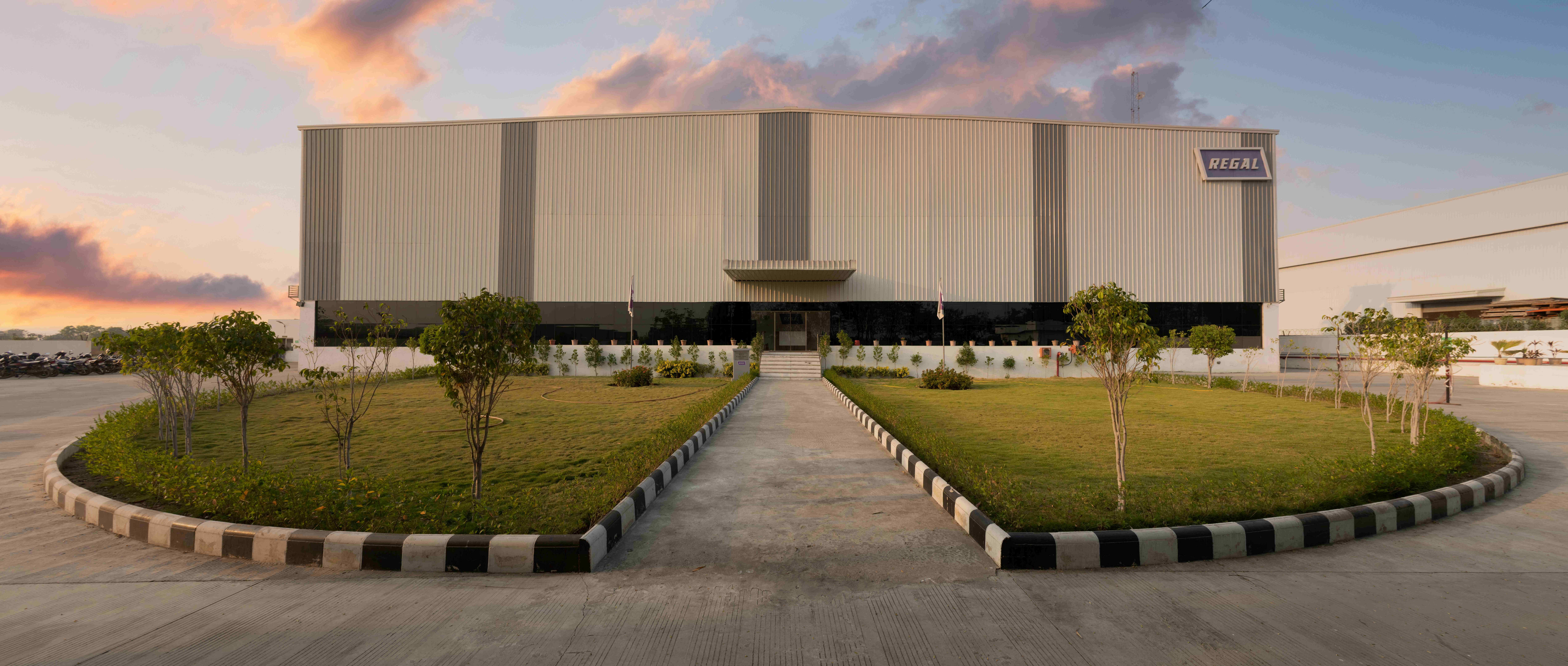
Why to sign up for a newsletter
Open