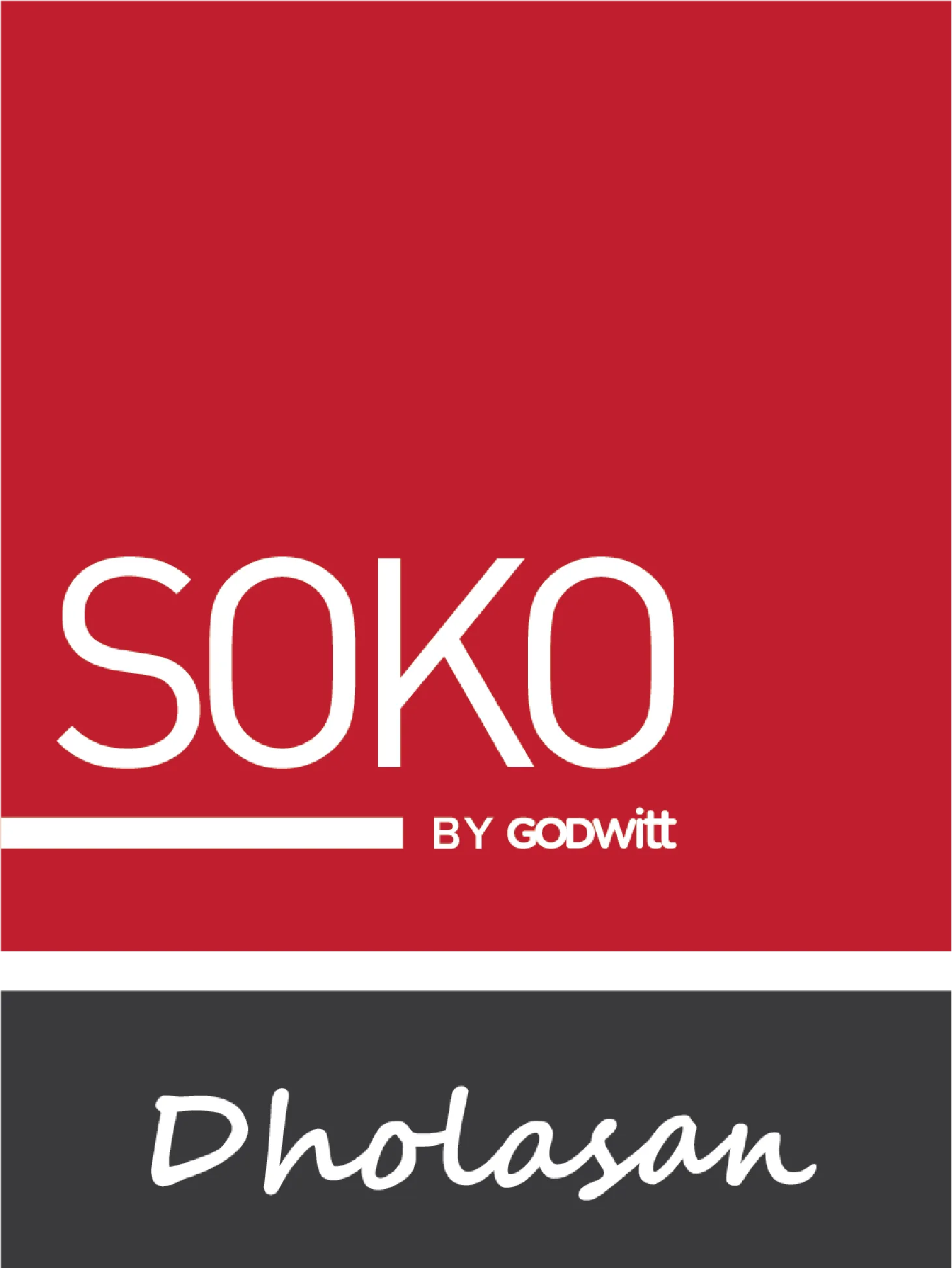
Heading
Project area
2.2 acres
Built up potential
7000+ pallet positions
Get to know the Facility
know more
Heading
Nestled in Mehsana, Gujarat, Soko by Godwitt – Dholasan is a facility that has redefined temperature-controlled storage in India. As India’s first temperature-controlled vertical ASRS facility outside of captive use, it combines state-of-the-art automation with precision engineering to set a benchmark in cold chain logistics.
Revolutionizing Cold Storage
Designed to operate like clockwork, this facility maintains precise temperatures across zones -25°C for storage, -5°C for sorting, and 5°C for transitory handling. Features like high-speed roll-up doors and nitrogen-based oxygen reduction systems ensure safety, consistency, and unmatched operational efficiency. With automated systems capable of handling 65 pallets per hour, the facility operates 4X faster than conventional warehouses, ensuring seamless operations with minimal human intervention.
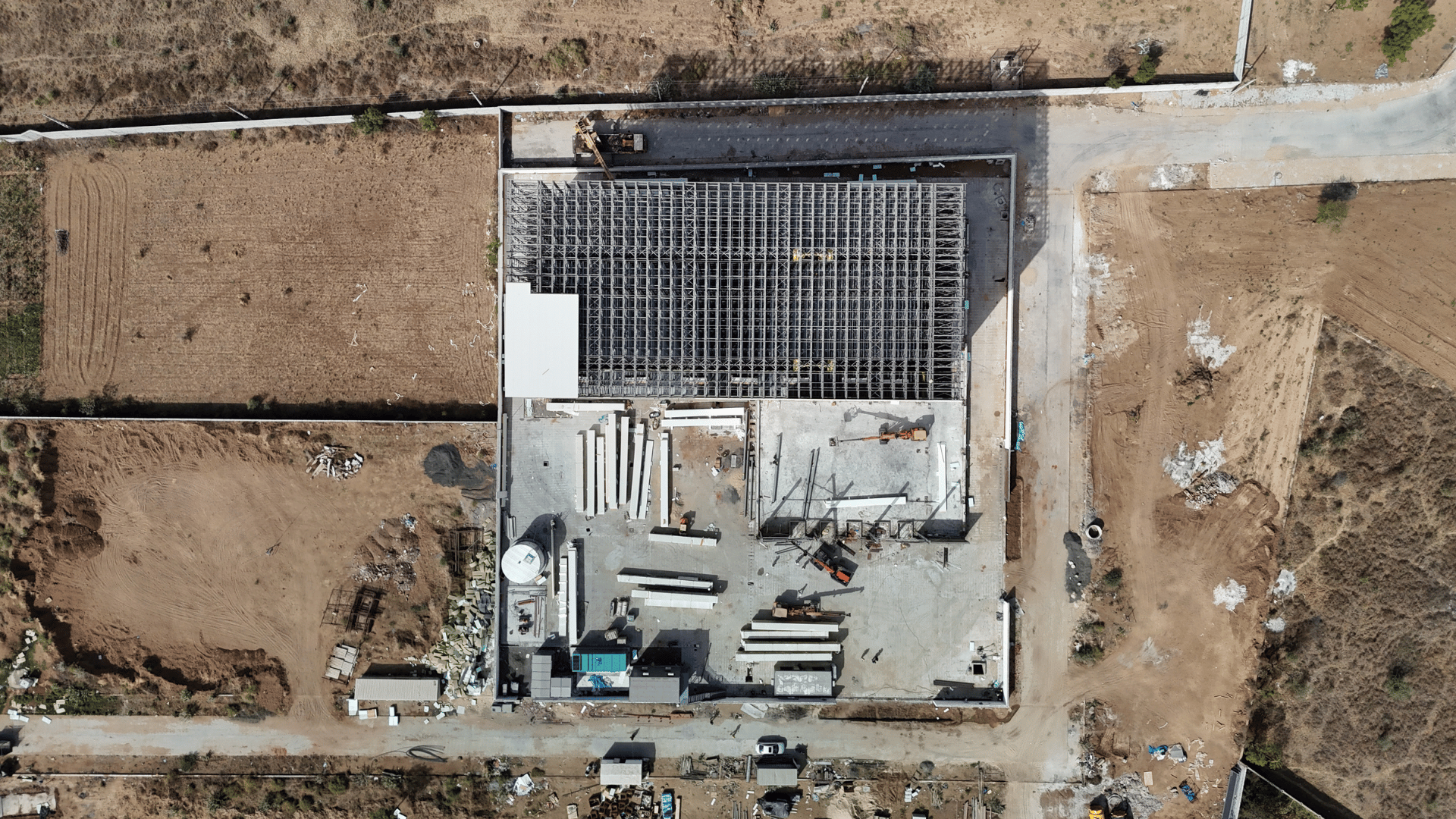
Development Journal
know more
Building Soko by Godwitt – Dholasan wasn’t just about constructing a temperature-controlled storage facility: it was about overcoming the challenges that come with creating something new in India’s cold chain logistics. The project began with a clear objective: to provide a reliable solution for temperature-sensitive goods. But we knew from the start it wouldn’t be easy.
From the regulatory hurdles to technical complexities, the path was full of learning curves. The construction phase brought its own set of challenges, including working in extreme temperatures, but we stayed focused on building a facility that was both efficient and safe.
To address the cooling of the facility, we relied on an eco-friendly Freon-based cooling system, chosen for its precise climate regulation across different zones and lower environmental impact compared to traditional refrigerants. To improve safety, we introduced a nitrogen-infused oxygen reduction system in the high bay area, reducing the risk of fire.
We also solved long-term flooring issues by installing heating cables beneath the RCC foundation to prevent moisture-related instability caused by sub-zero temperatures.
Through careful planning, engineering, and collaboration, we created a facility capable of handling 65 pallets per hour, with over 7,000 pallet positions.
Here’s how to get to the site
know more
This location is optimally located to serve you better
State Highway 410.62km
Ahmedabad Railway Station: 26km
Ahmedabad International Airport
57km
Kandla Port
308km
What makes this building a class apart
know more
Structure
Rack-clad temperature-controlled storage facility with a height of 33 meters.
Flooring
We installed heating cables beneath the RCC foundation to ensure insulated flooring and prevent frosting caused by constant sub-zero temperatures (-10 to -25°C). This solution protects the structure from moisture-related instability, ensuring long-term durability.
Insulation
PUFF Panel facility, servicing temperature-controlled areas with temperatures of -25 deg.Cel
Throughput: Maximizing Efficiency in Every Move
At Soko by Godwitt – Dholasan, we’ve designed the facility to handle a throughput of 65 pallet operations per hour—ensuring rapid and efficient movement of goods. This is achieved through:
5 docks with sectional doors, each equipped with radius-lip docks for smooth loading and unloading.
Levelers to boost operational efficiency by maintaining proper alignment for seamless pallet transfers.
A feed pallet conveyor connecting the low and high bays, streamlining the flow of goods throughout the facility.
2 stacker cranes capable of handling pallets up to 1 tonne, ensuring safe and efficient vertical storage.
Together, these features work in harmony to enhance speed, minimize delays, and maintain optimal performance across the facility.
Material handling
- Low Bay Area (5°C): A non-automated zone for temporary storage, sorting, and pallet handling. Goods move here from the ante-room before final dispatch.
- Ante Room (-5°C): Designed for transitory material handling, this area acts as a milestone for goods exiting the high bay. It prevents damage by gradually transitioning goods from -25°C to higher temperatures.
- High Bay Area (-25°C): Built for long-term storage, this automated zone houses over 7,000+ pallet positions, ensuring optimal conditions for temperature-sensitive goods.
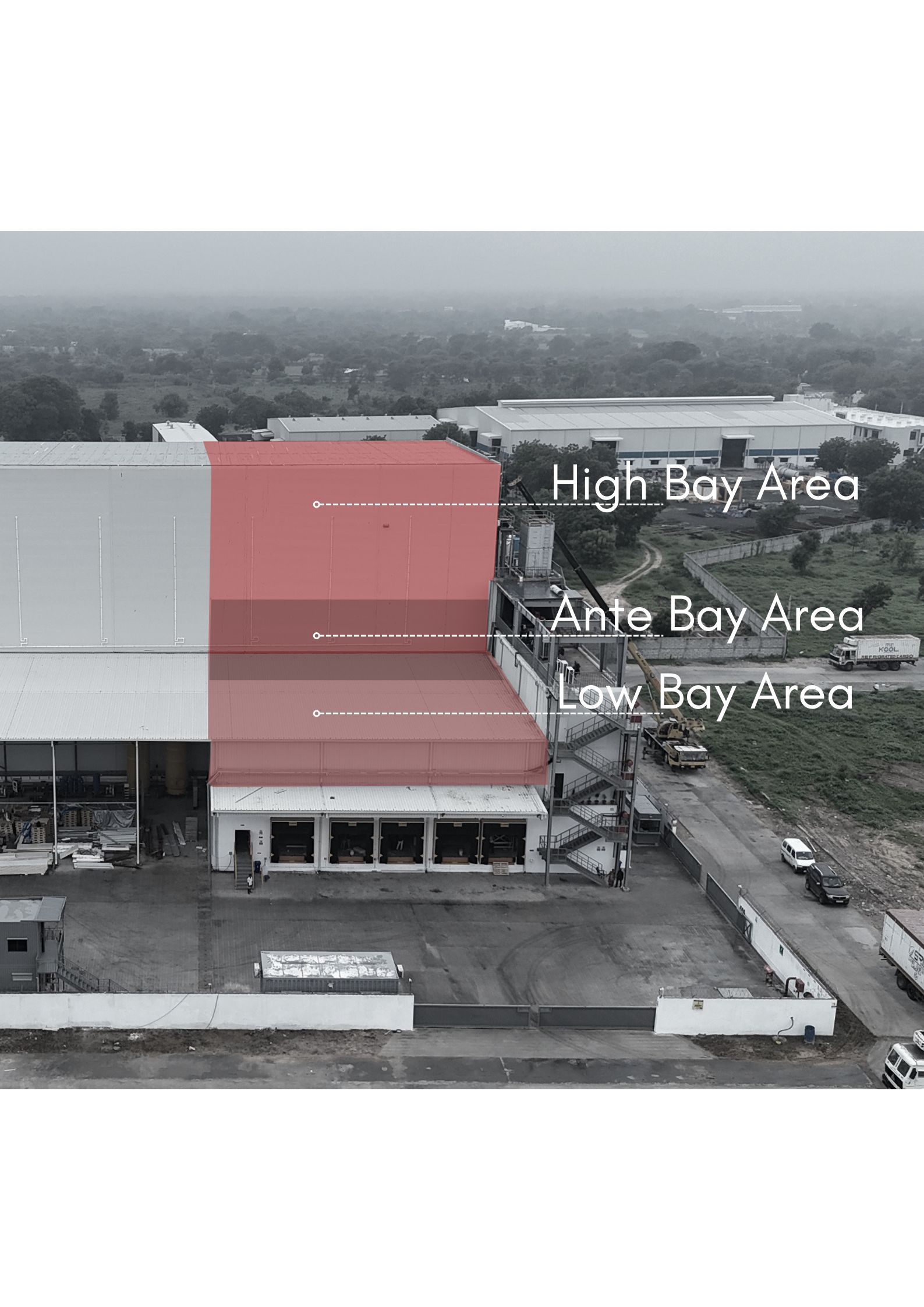
Fire prevention infrastructure
The facility features hose reels and fire hydrants, continuously monitored and pressurized 24/7. A laser-based aspirating smoke detection system in the low bay enhances early fire prevention, while the high bay utilizes an oxygen reduction system with nitrogen infusion to minimize fire risks by suppressing sparks and their spread.
Cooling methodology
The facility uses a Freon-based cooling system for precise and efficient temperature control across all zones.
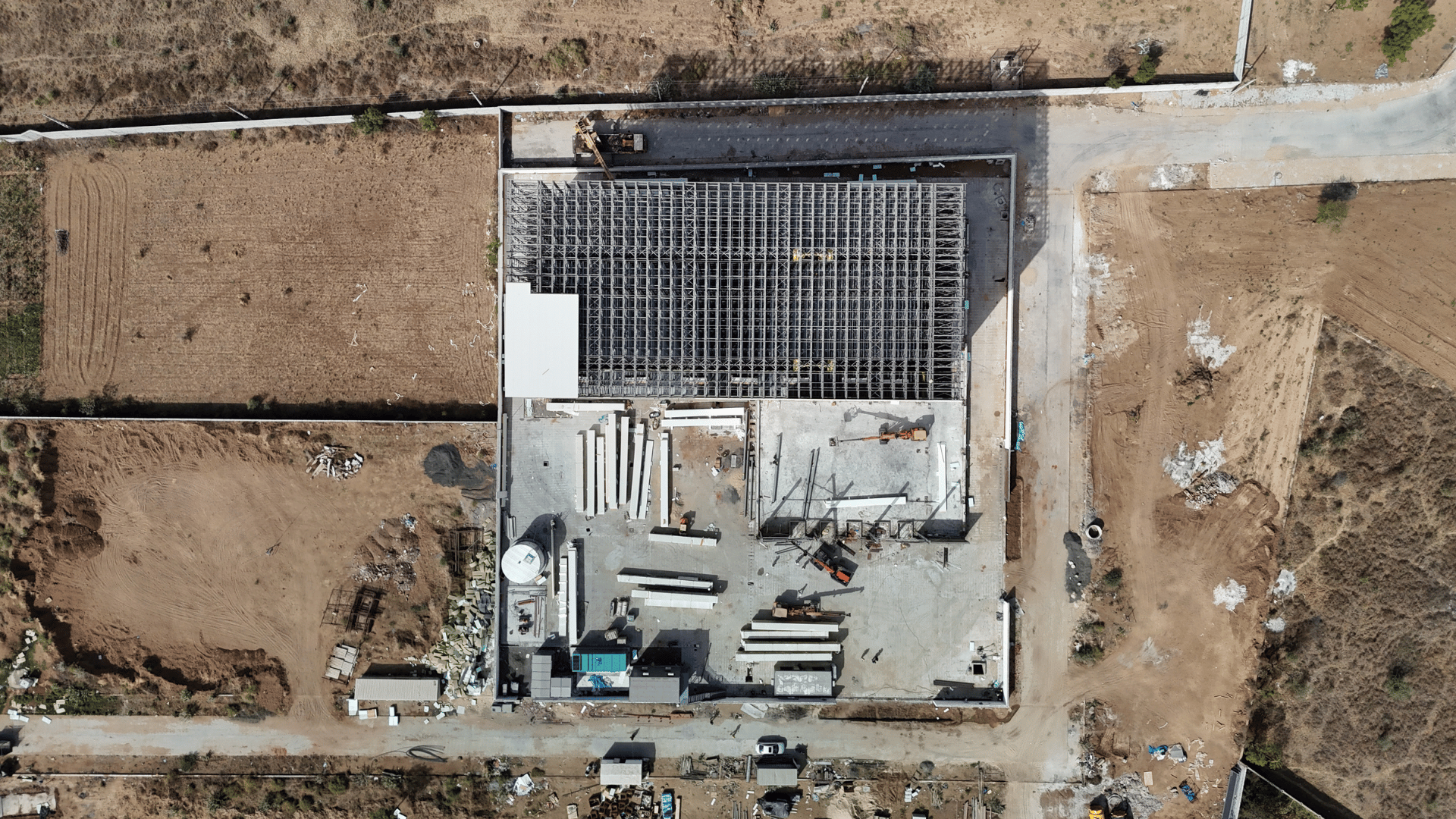
Why to sign up for a newsletter
Open