How We Maintain High-Performing Industrial Parks for Our Occupiers
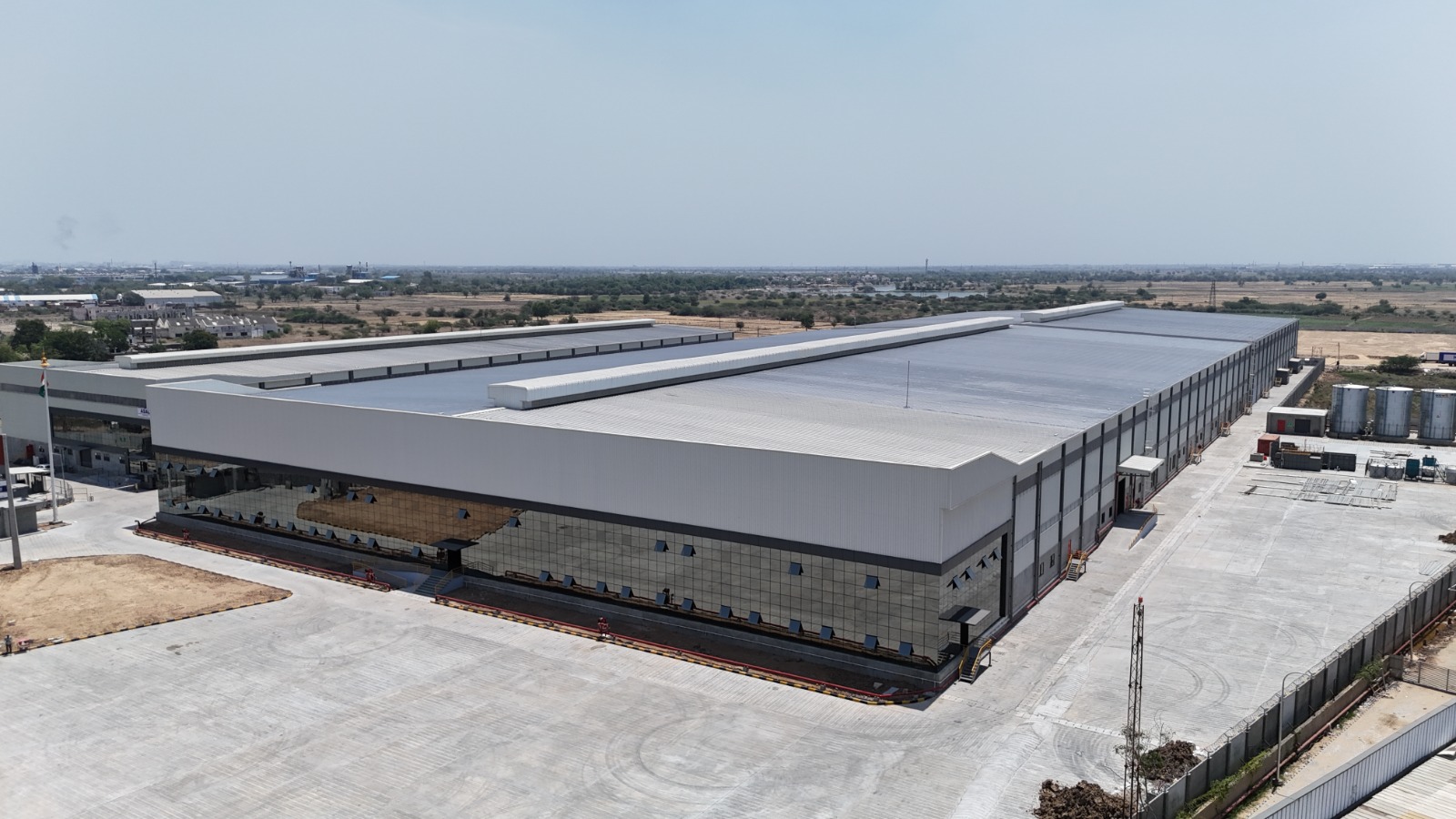
An industrial park isn’t just a collection of buildings and roads—it’s a living, breathing ecosystem that must function with efficiency, security, and long-term sustainability.
At Godwitt Construction, we go beyond just developing industrial spaces; we ensure that they remain high-performing hubs that support businesses in their day-to-day operations and long-term growth.
For companies operating in manufacturing, logistics, and warehousing, the quality of infrastructure, reliability of utilities, and ease of movement within an industrial park can significantly impact productivity.
So, how do we ensure that our industrial park remains future-ready and business-friendly?
Built for Efficiency: Infrastructure That Works, Always
A high-functioning industrial park starts with a robust, well-planned infrastructure that supports seamless operations for businesses of all sizes. At Godwitt, we ensure smooth, uninterrupted operations for our occupiers by providing RCC roads, smart stormwater drainage, ample parking space, and world-class security and surveillance.
- RCC Roads for High-Performance Logistics: Smooth and durable roads are essential for an industrial park. RCC roads are designed to handle heavy truckloads and continuous logistics movement without premature wear and tear.
- Stormwater Drainage to Prevent Waterlogging: Our stormwater drainage systems use historical rainfall data to efficiently redirect excess water—keeping roads and facilities clear even during heavy monsoons.
- Secure Perimeters & Controlled Access: We’ve put security measures in place that balance protection with accessibility, ensuring that only authorized personnel and vehicles enter. Our security features include 2.4m high compound walls, reinforced with 600mm barbed wire. Gated entry & exit points equipped with boom barriers for streamlined vehicle movement.
- Optimized Parking for Maximum Efficiency: A critical part of well-planned logistics is organized parking space. It eliminates operational bottlenecks caused by inefficient vehicle movement, allowing easy and quick access to facilities. We ensure one truck parking spot per 10,000 sq. ft. leased, allowing smooth loading and unloading. Dedicated four-wheeler and two-wheeler parking, preventing congestion with visitor zones for seamless accessibility.
Water: Managed Smartly, Used Sustainably
Water is a critical resource for any industrial operation, and at Godwitt Construction, we take a sustainable, efficiency-driven approach to managing it. Our industrial parks are designed to conserve, recycle, and optimize water usage,
- Rainwater Harvesting: Our parks are designed with recharge borewells that capture and store rainwater, replenishing groundwater levels and reducing dependency on external water sources. This ensures that occupiers have access to sustainable water reserves, even during peak operational periods. It reduces costs while enhancing long-term water security.
- STP Treated Water Recycling: To further optimize water usage, we implement Sewage Treatment Plants (STPs) across our industrial parks. This ensures that wastewater is treated, recycled, and repurposed for non-potable applications.
How does this benefit occupiers?
- 1,000 liters/day of treated water is allocated for washroom facilities, ensuring responsible domestic water usage.
- Recycled water is available at economical rates, providing cost-effective water solutions for operational needs.
- Any excess treated water is used for irrigation, promoting sustainable landscaping without additional water consumption.
- Strict TDS Monitoring: Quality control is essential when it comes to water usage. We conduct regular Total Dissolved Solids (TDS) monitoring, ensuring that all water used within our parks—whether for operations, domestic purposes, or landscaping—meets regulatory and operational standards.
Power & Fire Safety: Built for Reliability, Prepared for Emergencies
A high-performing industrial park needs an uninterrupted power supply and robust fire safety systems to keep operations running smoothly and securely. We prioritize both so that our occupiers can operate with confidence and peace of mind.
- Uninterrupted Power Supply: Industrial operations require stable, high-capacity power to function efficiently. To eliminate the risk of downtime, we provide:
- LT Power Connection with redundancy planning, ensuring occupiers have a stable power source.
- Backup power solutions to prevent disruptions in case of grid failures.
- Regular electrical system maintenance is carried out by Godwiitt on-site maintenance team to ensure long-term reliability and performance.
- Fire Safety Systems: Fire hazards are a serious risk in industrial environments. That’s why we’ve implemented a comprehensive fire safety infrastructure that meets National Building Code (NBC) guidelines and local safety regulations.
- Fire Safety Infrastructure: Fire Hydrant Systems are installed at strategic locations for immediate emergency response. Fire hose reels are installed inside the facilities for interior fire emergencies.
- Pressurized Fire Prevention System: Fire hydrants and hose reels are pressurized 24/7 for immediate response. We take special care to ensure that water tanks supplying fire prevention infrastructure are always kept full—spillover water is diverted to domestic use tanks, ensuring automatic refilling.
- Emergency Exits: Facilities are designed with emergency exits every 30 meters, strictly following safety norms. Emergency exit doors have a 120-minute fire rating and lead to staircases with hand railings as per regulations.
- Maintenance: Routine pressure checks and fire drills to ensure systems remain fully functional. Regular maintenance and upgrades to keep fire safety infrastructure up to date.
- Redundant Water Pump System: A redundant pumping system supports fire-safety water tanks which includes the main pump, the electric pump (backup), and the diesel pump (for electrical failures).
Green Spaces & Common Areas: Enhancing the Work Environment
- Perimeter Landscaping & Green Belts: Our parks are planned with Lush green belts around the perimeter, reducing dust and improving air quality. Automated irrigation systems to maintain landscapes with minimal water waste.Tree-lined internal roads that provide shade and enhance visual appeal.
- Miyawaki Plantations: Use only indigenous plant species, ensuring low maintenance and high adaptability. They grow 10 times faster than traditional plantations, improving air quality and biodiversity, and making the park more eco-friendly.
- Well-Planned Common Areas: A well-designed industrial park should also provide thoughtfully planned spaces for workers and visitors. We integrate common areas into our parks that make them feel organized, efficient, and welcoming—not just functional.
Proactive Management & Continuous Upgrades
A well-maintained facility isn’t just about aesthetics; it’s about preventing disruptions, reducing downtime, and ensuring long-term operational efficiency.
- 24x7 CCTV Surveillance: Industrial operations run around the clock, and so does our security. We maintain comprehensive CCTV surveillance across all common infrastructure
- Dedicated On-Site Teams: Our on-site maintenance teams ensure that daily operations run seamlessly, handling regular infrastructure checks to prevent potential issues. Immediate response to maintenance requests, ensuring minimal downtime. Facility management that adapts to occupiers’ needs. This proactive approach means that problems are solved before they become disruptions.
- Constant Upgrades & Repairs: We believe in continuous improvement, which is why we upgrade facilities regularly to meet the latest industrial standards. Perform preventive maintenance to reduce long-term wear and tear. Enhance existing infrastructure to adapt to new technology and operational needs.
- Immediate Maintenance Response: Downtime is costly. That’s why we have a rapid-response maintenance protocol, ensuring that any issue—whether it’s a structural repair, electrical fault, or general wear and tear—is addressed immediately.
Built for Today, Ready for Tomorrow
Through constant improvements, preventive maintenance, and future-ready upgrades, we create industrial ecosystems that operate seamlessly, evolve with business needs, and stay ahead of industry standards.
Every Godwitt park is designed to be secure, efficient, and adaptable, providing our occupiers with an environment where they can thrive without disruptions. By combining top-tier facilities with proactive management, we ensure that our parks remain high-performing industrial hubs—year after year.
Why to sign up for a newsletter
Open